Selecting the right OEM industrial scaffolding tools is crucial for ensuring safety, enhancing productivity, and achieving cost-effectiveness on construction sites. Having achieved substantial experience in the scaffolding industry, I can attest that these tool selections should be predicated upon several critical factors such as the nature of the construction project, compliance with safety standards, and the technological advancements embedded in the tools.
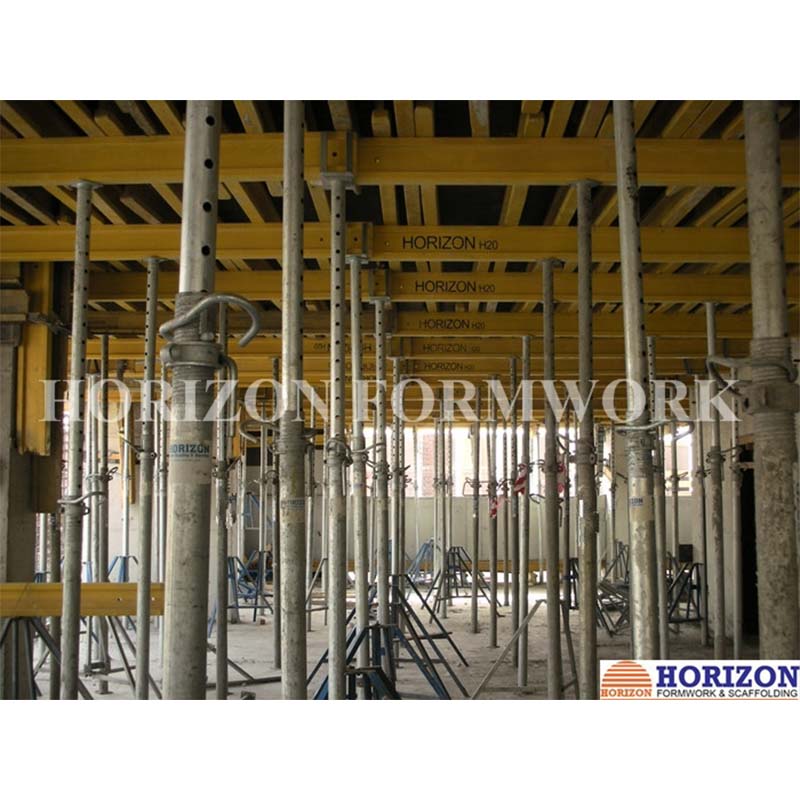
First and foremost,
safety cannot be overstated in the realm of industrial scaffolding. When evaluating OEM scaffolding tools, consider those that comply with industry safety regulations such as OSHA or EN requirements. The best tools are typically those that enhance worker safety while minimizing the risk of accidents. For instance, scaffolding tools composed of alloys such as titanium or reinforced steel offer increased durability and can withstand substantial weight loads, thus preventing spontaneous collapses and safeguarding the workforce.
In addition to safety, the efficiency of scaffolding tools is pivotal in advancing the overall productivity of a construction site. A variety of scaffolding systems, ranging from tube and coupler to prefabricated modular systems, demand bespoke tools. Utilizing OEM tools designed specifically for these systems ensures precise fits, ease of assembly, and swift disassembly, which can dramatically abbreviate project timelines. For example, Allen wrenches specifically sized for scaffold bolts or custom torque tools can expedite structural assembly and adjustments, thus optimizing labor efficiency.
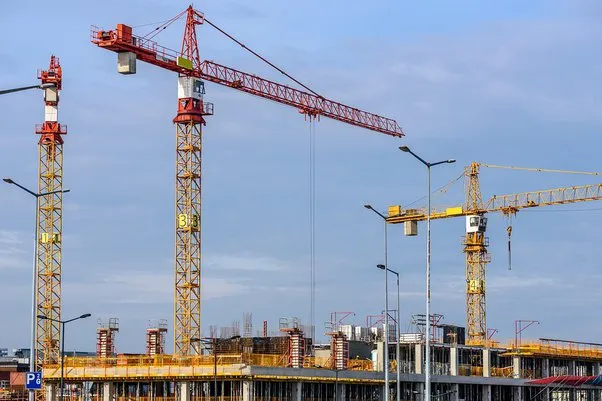
The professional expertise embedded in OEM manufacturing further underscores the importance of selecting specialized industrial scaffolding tools. Manufacturers who possess intimate knowledge of scaffolding engineering are more apt to produce tools that not only satisfy but exceed project expectations. They often engage in rigorous testing protocols to ensure tools operate optimally under various environmental conditions, ensuring they retain functionality whether on a high-rise urban project in windy conditions or a complex oil rig infrastructure.
oem industrial scaffolding tools
Moreover, as technology progresses, so too does the sophistication of scaffolding tools. Modern OEM providers are integrating smart technologies into their products, such as sensors that monitor structural integrity or RFID tracking systems that prevent tool loss on sprawling construction sites. These technological attributes not only bolster safety but also foster accountability and operational efficiency.
The authoritative voice of trusted OEMs also lends a significant advantage when considering warranty and support services. Renowned manufacturers stand by their products, offering comprehensive support packages and extended warranties. This not only provides peace of mind but also assures the buyer of the long-term return on investment, as reliable tools require less frequent replacements and maintenance.
Finally, an exploration of the track record of an OEM provider, including customer testimonials and case studies, is advisable. These external endorsements serve as a benchmark for trustworthy service, evidenced by successful project outcomes in diverse conditions. Engaging with suppliers who have a proven trajectory of delivering high-quality scaffolding solutions underlines the trustworthiness imperative.
In conclusion, choosing OEM industrial scaffolding tools goes beyond mere functional requirements; it involves a multifaceted evaluation of safety, expertise, technological integration, authoritative backing, and trustworthiness. By aligning these factors with your project needs, you can foster an environment that not only thrives on efficiency and precision but also prioritizes the well-being of its workforce, thereby paving the way for successful project completions and long-term industrial progress.