Properly removing formwork from columns is pivotal in ensuring structural integrity and maintaining project timelines. This process can be intricate, requiring a deep understanding of materials, environmental conditions, and adherence to safety standards. As a seasoned engineer with decades of field experience, let me elucidate the nuances of formwork removal, drawing from real-world applications and industry best practices.
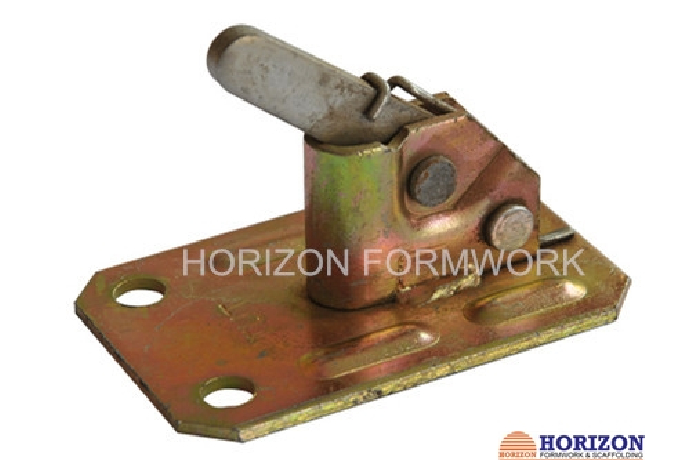
Formwork, often regarded as the backbone of construction, demands meticulous planning and execution. Its removal, particularly for columns, is not merely a technical procedure but an art that balances timing, material strength, and environmental factors. Done prematurely, it could spell disaster, compromising the column’s structural stability. On the other hand, excessive delay means increased project costs and logistical hurdles.
A cornerstone of effective formwork removal involves understanding the curing process of concrete. Concrete doesn’t reach its full strength instantaneously; it is a gradual process affected by mix proportions, temperature, humidity, and other environmental conditions. For columns, this requires close monitoring to hit the optimum strength threshold before dismantling the formwork. Typically, a concrete column achieves sufficient strength to support its weight and additional construction loads within 48 to 72 hours under ideal conditions. Nevertheless, variations in environmental factors and mix design can extend this timeframe.
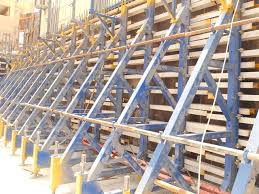
In the application of OEM solutions for formwork, precision engineering and material science converge. The latest OEM formwork systems are designed to facilitate accelerated curing, employing advanced materials that offer enhanced thermal insulation. These systems also incorporate complex geometric designs, ensuring minimal adherence to concrete and thereby simplifying the removal process. Leveraging such innovations not only streamlines the workflow but also reinforces safety by reducing the risk of structural failures due to human error.
oem removal of formwork for column
Another critical aspect is the employment of non-destructive testing methods to assess the concrete’s strength before formwork removal. Tools such as rebound hammers, ultrasonic pulse velocity tests, and maturity meters provide quantifiable data to make informed decisions. Integrating these assessments into the schedule ensures that the formwork is removed only when the concrete is at an optimal strength, thereby aligning with both the engineering specifications and safety guidelines.
Moreover, compliance with local regulations and international standards cannot be overemphasized. The field is regulated by stringent norms that dictate not just when, but how formworks should be dismantled. Ensuring alignment with these standards is not only a testament to a contractor's professionalism but also a mechanism to safeguard the workforce and the final structure.
The step-by-step dismantling process remains crucial. It requires skilled labor familiar with the machinery and techniques to prevent any undue stress on the structure. Training and competence of the workforce in handling cutting-edge OEM systems is fundamental.
In conclusion, the removal of formwork from columns is a critical phase that demands an expert blend of experience, precise timing, and advanced technology. As new materials and methods reshape the landscape, the focus should remain steadfast on safety and structural integrity. By harnessing the expertise from OEM innovations and industry standards, projects are not only delivered efficiently but also stand the test of time. This approach bestows any construction endeavor with the hallmark of trustworthiness and authority, attributes that are indispensable in today's competitive industry.