In the realm of modern construction techniques, OEM PP hollow formwork is revolutionizing the industry with its profound advantages and innovative qualities. Understanding the specific intricacies of this product, including its application, durability, and environmental impact, is crucial for construction professionals aiming to enhance structural integrity and efficiency.
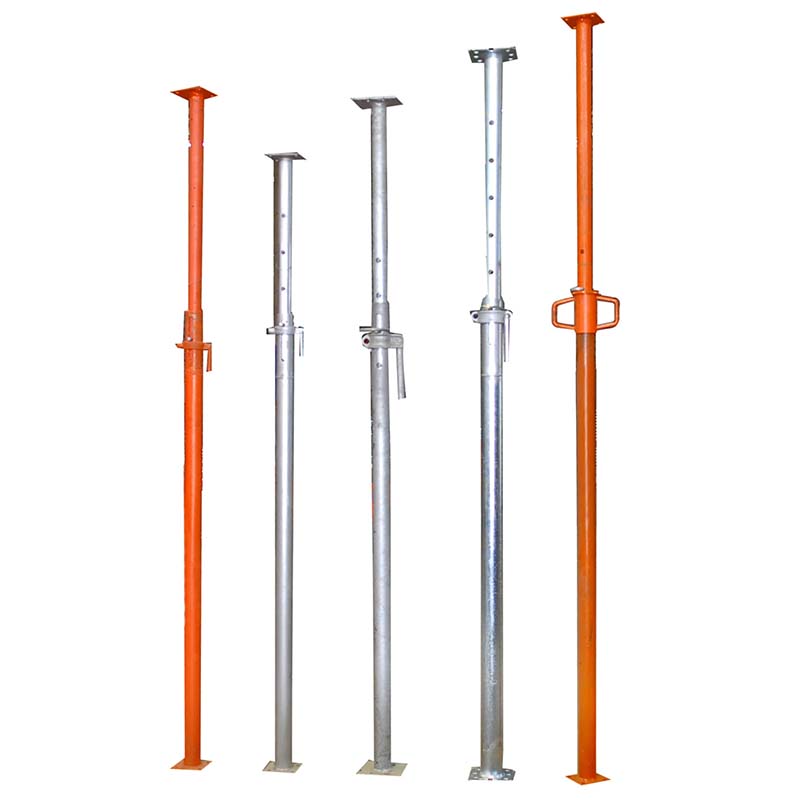
PP hollow formwork, constructed from polypropylene (PP), is gaining momentum due to its remarkable properties that address many of the inherent limitations found in traditional formwork systems. For builders and contractors, adopting OEM PP hollow formwork means embracing a new era of construction that promises sustainability, cost-effectiveness, and superior structural outcomes. Here, we delve into the core aspects of OEM PP hollow formwork that underline its efficacy and credibility.
Firstly, the lightweight nature of PP hollow formwork significantly enhances the ease of handling and installation. Traditional formwork materials, such as timber and metal, are cumbersome, often requiring additional labor and equipment to maneuver. In contrast, the reduced weight of PP hollow formwork aids in faster assembly and disassembly, thereby accelerating construction timelines and reducing labor costs. This benefit is particularly pronounced in large-scale projects where time efficiency translates to substantial financial savings.

The robustness and reusability of PP hollow formwork also contribute to its growing popularity. Designed to withstand multiple reuse cycles without degradation of quality, this formwork presents a cost-effective solution for contractors. It maintains its structural integrity under various conditions, which is vital for creating safe and reliable buildings. The ability to reuse formwork not only leads to economic savings but also minimizes waste, aligning with global sustainability goals by reducing the need for disposable materials.
A key aspect of PP hollow formwork is its resistance to environmental factors. Construction sites are susceptible to harsh weather conditions and varying temperatures, which can impact material longevity. However, PP hollow formwork boasts excellent water and chemical resistance, ensuring consistent performance regardless of ambient conditions. This resistance dramatically reduces maintenance requirements and enables formwork to be utilized in diverse geographic locations, further emphasizing its flexibility and reliability.
oem pp hollow formwork
Moreover, the innovation behind PP hollow formwork extends to its impact on structural properties. This formwork facilitates better heat insulation and acoustic performance, lending itself to applications where environmental control within buildings is critical. The inherent design of hollow formwork aids in optimizing the energy efficiency of structures, offering a tangible benefit in reducing long-term operational costs and energy consumption.
From a technical standpoint, the precision with which PP hollow formwork can be engineered is a testament to its suitability for complex architectural designs. Advanced manufacturing techniques ensure high dimensional accuracy and flexibility, allowing custom solutions tailored to specific project requirements. Such adaptability ensures that architects and engineers can achieve their design visions without compromise, further elevating the aesthetic and functional quality of construction projects.
In terms of environmental impact, PP hollow formwork stands as a beacon of modern sustainable practices. The reduction in natural resource consumption due to its longevity and reusability highlights a shift towards a circular economy in the construction sector. Moreover, the recyclability of the materials used in PP hollow formwork ensures minimal environmental footprints upon disposal, aligning with stringent environmental regulations and corporate responsibility policies.
For professionals seeking authoritative insights and practical applications of OEM PP hollow formwork, understanding these dynamics is crucial. Collaborations with manufacturers and ongoing training in the use of this innovative formwork are paramount to leverage its full potential. Additionally, keeping abreast of developments in materials science and construction technology will assist in capitalizing on the formwork’s capabilities.
In conclusion, OEM PP hollow formwork exemplifies a synthesis of engineering excellence and sustainability in modern construction. Its benefits extend beyond traditional metrics, promising improvements in safety, efficiency, and environmental stewardship. By adopting this next-generation formwork, construction stakeholders position themselves at the forefront of industry advancements, ensuring that structures are built to last while minimizing their ecological impact.